Guida illustrata progettazione magazzini automatici | New 11/17
Il Documento fornisce una panoramica normativa con illustrazioni per la progettazione di sicurezza dei magazzini automatici a corsie strette (VNA - Very Narrow Aisme).
Il Documento tratta i criteri di progetto generali, i sistemi di guida, le scaffalature, la pavimentazione, la tecnologia RFID, i sistemi di protezione individuale e l’ottimizzazione dei processi, check list finale e riferimenti normativi.
Il documento basato sull’Opsuscolo Magazzino a corsie strette VNA della Jungheinrich Italiana S.r.l, ne aggiorna i contenuti normativi nazionali IT e norme armonizzate/non in vigore, con estratti.
I magazzini a corsie strette permettono il massimo sfruttamento di spazio grazie alla drastica riduzione di larghezza delle corsie che unita alla possibilità di un’altezza più elevata di prelievo merce consente di incrementare notevolmente la capacità del magazzino. Uno dei vantaggi di tali sistemi è l’accesso diretto ad ogni posto pallet.
Se necessario è possibile effettuare operazioni di picking direttamente dallo scaffale.La merce può inoltre essere movimentata secondo il principio FIFO.
Tali magazzini consentono:
- la minimizzazione dello spazio necessario e massimizzazione della resa di movimentazione.
- un miglior sfruttamento possibile grazie all’interfacciamento ottimale tra carrello, scaffalatura e pavimentazione.
Download Documento Preview
Excursus
Guida meccanica e guida induttiva Al fine di ridurre al minimo lo spazio dei corridoi di movimentazione, la distanza tra i carrelli usati nelle corsie strette e lo scaffale è molto ridotta. La EN ISO 3691-3:2017 prescrive una distanza di sicurezza minima di 90 mm (tra carico prelevato e scaffale).
_____
EN ISO 3691-3:2017 .. 6.4 Installation information 6.4.1 The truck manufacturer shall provide the user with dimensional tolerances for the floor, clearance requirements for racking, and details of other interfacing equipment. 6.4.2 The truck manufacturer shall provide information to the (end) user that trucks operating in aisles with guidance systems shall have a designed minimum side clearance of not less than 90 mm between any elevating part of the truck, including the load and the racking or loads in the rack in their proper stacked position.
In funzione del sistema di guida, del tipo di carrello usato e della dimensione dei pallet possono rendersi necessarie delle distanze di sicurezza maggiori (es. con guida induttiva).I sistemi di guida garantiscono un funzionamento sicuro ed elevate rese di movimentazione. La guida meccanica consente di raggiungere elevate velocità di traslazione e di sollevamento e facilita il lavoro del conducente. ______ ...
Distanza di sicurezza per guida meccanica Una distanza di sicurezza di 100 mm per carrelli guidati con sistema meccanico consente di ottimizzare i risultati in termini di sicurezza e di resa di movimentazione. La distanza tra ruota di carico e guida deve essere almeno di 50 mm in modo da facilitare al conducente l’ingresso tra le guide e il corridoio.
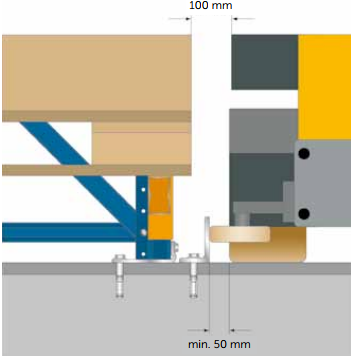
Figura 1 - Distanze di sicurezza per guida meccanica
Larghezza della corsia di lavoro per guida meccanica La larghezza minima della corsia di lavoro (AST) è calcolata tenendo conto della profondità di stoccaggio del carico, delle dimensioni di ingombro del mezzo utilizzato e delle distanze di sicurezza.
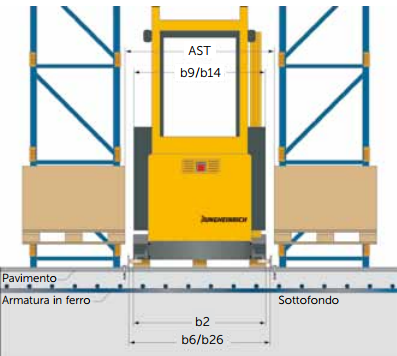
Figura 2 - Larghezza corsia per guida meccanica ....
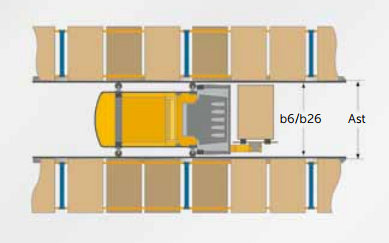 Figura 3 - Larghezza corsia per guida meccanicaLegenda
b2 - Larghezza asse di carico b6 - Scartamento esterno rulli b9/b14- Larghezza cabina/telaio carrello trilaterale b26 - Distanza minima tra le guide AST - Larghezza corsia di lavoro
... Montaggio delle guide Le guide vengono posate ed ancorate al pavimento medianti tasselli dedicati ad interassi differenziati in funzione delle forze che agiscono sulle varie zone della guida stessa. Gli interassi tra i tasselli possono infatti variare da 800÷1.000 mm ed essere ridotti fino a 300 mm circa nella zona di ingresso corsia. Le giunzioni delle guide vengono eseguite in loco mediante saldatura con conseguente finitura superficiale per assicurarne la protezione contro la corrosione.
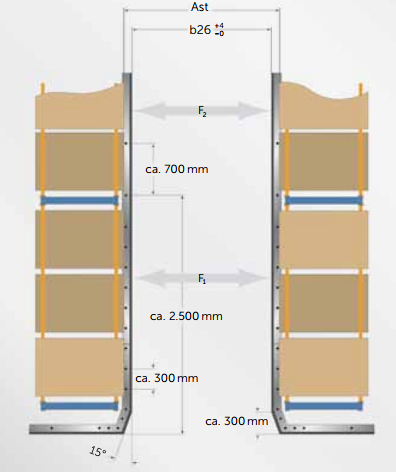
Figura 4 - Montaggio delle guide
Guida induttiva (filo guida)
Principio di funzionamento Il carrello guidato ad induzione segue la traccia di un filo conduttore posizionato al di sotto del pavimento. Un generatore di frequenza alimenta il filo conduttore che viene percorso da corrente alternata ad alta frequenza (bassa tensione).
La corrente genera un campo elettromagnetico concentrico.Speciali antenne montate sul carrello rilevano questo campo elettromagnetico e registrano ogni cambiamento di posizione del carrello rispetto al filo conduttore. In tal caso il carrello sterza automaticamente e si riporta in posizione. Il carrello è così guidato in maniera sicura lungo l’intera corsia.
Pavimento del fabbricato L’uso di armature di ferro o fibre di acciaio nel pavimento richiede i seguenti accorgimenti:
Per evitare influssi negativi sul campo elettromagnetico alternato, armature di ferro (reti elettrosaldate) devono essere collocate nel calcestruzzo, al di sotto del livello del filo conduttore. Una distanza maggiore di 50 mm tra filo conduttore e armatura si è rivelata ottimale. Se al posto delle reti si utilizzano fibre d’acciaio, è importante che vengano distribuite uniformemente nel calcestruzzo. La quantità di fibre nel calcestruzzo deve essere al massimo di 30 kg/m3. Inoltre è bene evitare, in un’area di ±250 mm dal filo conduttore, la presenza di altri componenti metallici, come ad esempio profili d’acciaio per la protezione da fughe di dilatazione e giunti.
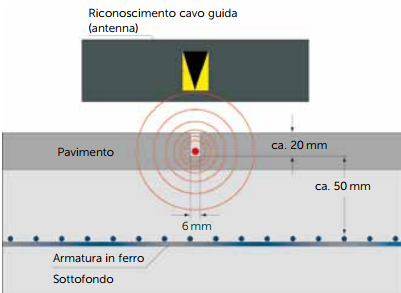 Figura 9 - Filo conduttore nel pavimento ... Layout del filo conduttore L’impianto per guida induttiva a pavimento è installato secondo la configurazione di un loop conduttore chiuso; le due estremità sono collegate con il generatore di frequenza (FG). In presenza di un numero dispari di corsie sarà necessario installare una linea di ritorno fino al generatore di frequenza. Per prevenire disturbi dei campi elettromagnetici nell’area di guida, si raccomanda di mantenere una distanza di 1,5 m tra fili della stessa frequenza, ad eccezione delle linee di ritorno che non vengono utilizzate per la circolazione. ...
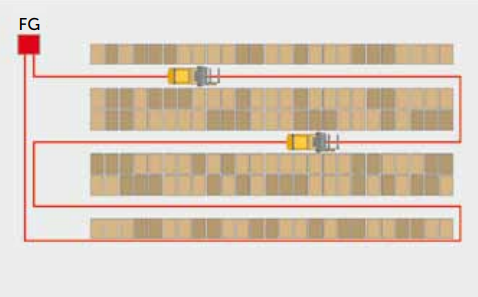 Figura 17 - Traiettoria del filo conduttore con un numero dispari di corsie
3. Scaffalature
Scaffalatura portapallet nei magazzini a corsie strette Esistono svariate tipologie di scaffalature. La loro struttura dipende dal tipo di impiego e dalle condizioni presenti in loco.
Vedi Documento Sicurezza magazzini a scaffalatura metalliche
Le grandezze più importanti da considerare per il dimensionamento di una scaffalatura sono i pallet o contenitori utilizzati, peso e dimensioni dei carichi ed i carrelli impiegati per servire gli scaffali. Nei sistemi a corsie strette si ricorre principalmente a scaffalature portapallet che possono essere monoposto o a più posti, a seconda del peso del carico. Le prove statiche sono effettuate in conformità alla norma
EN 15512 - Sistemi di stoccaggio statici in acciaio - Scaffalature regolabili porta pallet - Principi per la progettazione strutturale.
Le scaffalature porta-pallet sono realizzate in conformità alle seguenti norme:
EN 15620 - Sistemi di stoccaggio statici di acciaio - Scaffalature portapallet - Tolleranze, deformazioni e interspazi EN 15629 - Sistemi di stoccaggio statici di acciaio - Specifiche dell'attrezzatura di immagazzinaggio EN 15635 - Sistemi di stoccaggio statici di acciaio - Utilizzo e manutenzione dell'attrezzatura di immagazzinaggio
Non essendo una costruzione collegata direttamente con l’edificio, le scaffalature portapallet consentono un’elevata flessibilità di installazione.
Vantaggi delle scaffalature portapallet nei magazzini a corsie strette:
- Accesso diretto a tutti gli articoli - Libera assegnazione delle locazioni - Utilizzabili sia per impiego manuale che automatizzato - Possibilità di stoccaggio longitudinale trasversale o misto - Flessibilità di dimensionamento in funzione dei contenitori, dei pallet e dei carichi - Possibilità di realizzare il principio FIFO - Possibilità di effettuare le operazioni di picking direttamente dallo scaffale ...
Postazioni di carico/scarico - prestoccaggi Le postazioni di carico/scarico sono normalmente formate dai correnti sporgenti dell’ultima campata dello scaffale. L’ultima spalla prima dell’area di carico/scarico è meno profonda e consente quindi il montaggio dei correnti filanti. Le postazioni di carico/scarico vengono equipaggiate con dispositivi o telai di centraggio. I carrelli di servizio a guida libera scaricano quindi i carichi in una posizione prestabilita dove vengono presi in consegna dai carrelli usati nelle corsie strette. Per l’impiego di roll container, l’ultima postazione di carico scarico è realizzata come «docking station». I roll container possono essere spinti manualmente nella postazione di carico/scarico. Un apposito fermo ancorato nel pavimento e integrato nello scaffale provvede al centraggio del container.
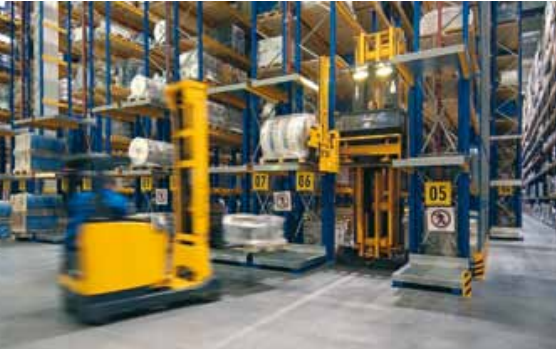
Figura 22 - Carico/scarico su scaffalatura cantilever separata ... Distanze di sicurezza - Spazi liberi nella scaffalatura La norma EN 15620 definisce gli spazi liberi come segue: «Gli spazi liberi sono le misure nominali necessarie per le distanze tra i componenti mobili e fissi del sistema che devono poter evitare un urto anche in presenza di una combinazione sfavorevole di tutte le tolleranze importanti ed eventuali deformazioni.»
Simili distanze sono ad esempio: - Distanze fra i carichi (x2) - Distanza dai montanti della scaffalatura (x1) - Distanza dai correnti superiori (y) - Distanza dai vari impianti tecnici e costruttivi (sprinkler, tubature, illuminazione, pilastri, ecc.)
Condizioni da considerare per il dimensionamento delle distanze: - Peso e dimensioni dei carichi - Livello di altezza del corrente superiore dello scaffale - Tipologia dei carrelli usati per servire il magazzino a corsie strette (sistema Man-up o Man-down) - Grado di automazione dei carrelli - Dispositivi ausiliari impiegati (preselezione dell’altezza di sollevamento, sistema automatico di stoccaggio e prelievo)
Gli spazi liberi sono tutti da intendersi come distanze minime. Le distanze possono inoltre essere disciplinate, in ogni specifico caso, dalle direttive e dalle norme vigenti nel luogo d’impiego.
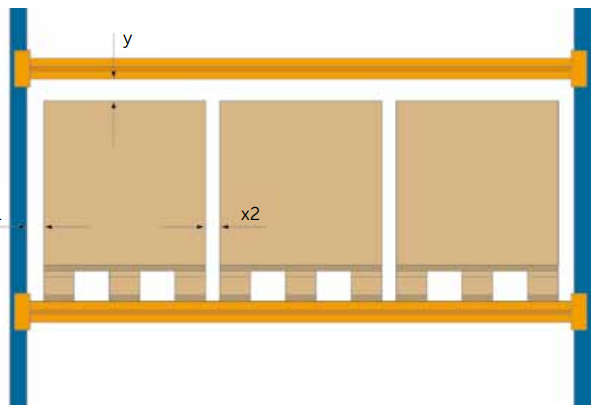
Figura 25 - Distanze di sicurezza ... Vie di fuga e di soccorso La distanza da un qualsiasi punto all’interno del magazzino al prossimo compartimento antincendio o all’esterno non deve essere superiore a 30 m (in linea d’aria) ovvero a 50 m di percorso a piedi. Tale distanza può variare in base ai regolamenti dei singoli paesi. Se per non superare la distanza massima si rende necessaria una via di fuga trasversale attraverso l’impianto di scaffalature, bisogna considerare i seguenti criteri:
- Secondo le normative vigenti sul luogo di lavoro, la larghezza delle vie di fuga va calcolata in funzione del grado di affollamento.
- La larghezza libera della corsia per attività normali deve essere di almeno 0,80 m (DM 10 marzo 1998) e di almeno 1,20 m per attività soggette a CPI (Certificato Prevenzione Incendi - DPR 151/2011).
- L’altezza libera non deve essere inferiore ai 2,00 m.
- Va inoltre impedito l’uso improprio delle vie di fuga da parte del personale.Appositi cartelli di segnalazione dovranno essere predisposti per impedire che le vie di fuga vengano ostruite.Sulla base del posizionamento delle uscite di sicurezza in relazione al layout delle scaffalature, saranno predisposte eventuali vie di fuga trasversali all’interno della scaffalatura.
Tali passaggi dovranno essere opportunamente protetti contro una possibile caduta delle unità di carico.
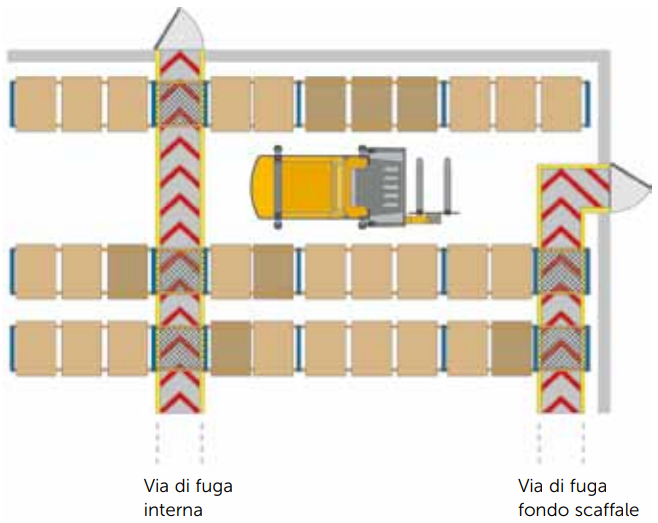 Figura 29 - Vie di fuga
Aree di protezione suddivise per classe d’incendio Per il corretto dimensionamento di un impianto sprinkler occorre prima stabilire la classe d’incendio, facendo riferimento ad EN 12845:2015 (progettazione ed installazione di impianti sprinkler). Gli edifici e le aree da proteggere vanno suddivisi per classi di pericolo in base alla loro tipologia d’impiego e ai rischi d’incendio cui sono esposti:
LH - Basso rischio d’incendio OH - Medio rischio d’incendio Le aree di protezione vengono suddivise in quattro classi di pericolo (OH1–OH4) HHP - Elevato rischio d’incendio, rischi inerenti alla produzione. Le aree di protezione vengono suddivise in quattro classi di pericolo (HHP1–HHP4) HHS - Elevato rischio d’incendio, rischi inerenti allo stoccaggio
Le aree di protezione vengono suddivise in quattro classi di pericolo (HHS1–HHS4). ... 4. PavimentazioneStruttura e requisiti Le caratteristiche della pavimentazione industriale, soprattutto la sua planarità, condizionano in maniera decisiva il funzionamento e l’efficienza di un magazzino a corsie strette. Lo strato portante e la soletta di base vanno dimensionati in modo tale che in presenza di carichi non vengano superate le tolleranze ammissibili.
Struttura La pavimentazione industriale è normalmente costituita da un sottofondo, da uno strato portante di calcestruzzo e da uno strato di finitura (massetto). Gli strati sottostanti allo strato di calcestruzzo servono, ad esempio, al costipamento del sottofondo, alla protezione contro l’umidità e all’isolamento termico.
Requisiti Per quanto riguarda la resistenza, lo strato di copertura (massetto) deve soddisfare i requisiti della classe di carico II prevista dalla norma EN 13813.
Sotto carico il pavimento non deve presentare deformazioni plastiche. Pozzetti, canali o simili interruzioni del pavimento devono essere disposti ad una distanza di almeno 200 mm dalle corsie di circolazione. Simili costruzioni e installazioni sono da evitarsi nella corsia di lavoro. La pavimentazione deve essere resistente ad oli e grassi e quindi priva di untuosità. Il rivestimento delle corsie adibite alla circolazione deve essere resistente all’abrasione e non tendere alla formazione di polvere.La resistenza di messa a terra secondo la norma EN 1081 non deve essere superiore a 106 Ohm.
La distanza di frenatura deve essere conforme alla norma 15160 – parte 1
L’aderenza del pavimento deve essere conforme alla norma ISO 6292 (valore empirico: ca. 0,5 µ).
Si veda
DIN 18202 (cfr. Tabella 1)
Direttiva VDMA: Requisiti pavimentazione per carrelli da corsia stretta (IT) ...
6. Tecnologia RFIDTecnologia transponder
- Informazioni sul comando di veicoli per corsia stretta - Sistema a pavimento e comunicazione con l’ambiente magazzino - Diversi collegamenti e profili di velocità
Transponder come supporto informazioni Il comando dei veicoli nelle corsie strette e nelle aree del magazzino è un criterio decisivo per un funzionamento sicuro e per il mantenimento di tutte le funzioni richieste, come rallentamento di fine corsia, interruzioni di sollevamento o riduzioni di velocità. I sistemi normalmente reperibili in commercio utilizzano per tale comando soprattutto magneti a pavimento o elementi riflettenti. Mediante diverse «combinazioni di magneti» è possibile riconoscere diverse zone ed eseguire meccanicamente commutazioni di sicurezza appropriate - ad es. uno stop automatico del veicolo prima dell’uscita dalla corsia.
Con questi interruttori ottici o meccanici è tuttavia possibile trasmettere al carrello soltanto un numero di informazioni limitato. Sono disponibili al massimo tre tracce. Questo tuttavia non è sufficiente per gli impianti esistenti sempre più complessi e per i requisiti di sicurezza sempre crescenti. Per il comando dei veicoli da corsia stretta, noi impieghiamo transponder delle sole dimensioni di 9x16 mm che vengono installati nel pavimento del capannone ad una distanza di max. 10 m l’uno dall’altro. Il veicolo stesso è dotato di un dispositivo RFID di lettura e scrittura che comunica con i transponder, richiamando e utilizzando le seguenti informazioni:
- Identificazione del numero e del tipo di corsia - Referenziamento della misurazione della distanza all’interno delle corsie ...
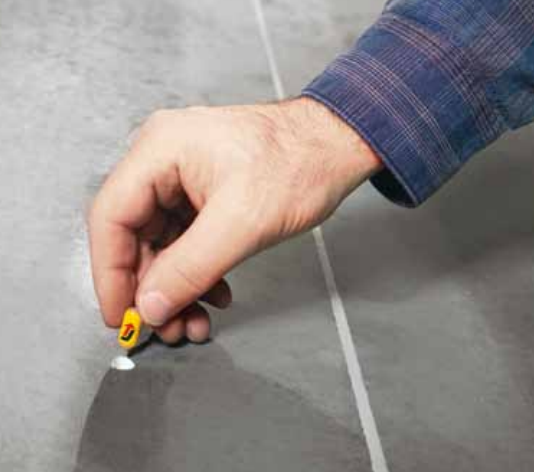 Figura 48 - Trasponder ...
7. Sistemi di protezione individuale (PSS)Fondamenti giuridici La sosta contemporanea di pedoni e mezzi di movimentazione all’interno di una corsia stretta è generalmente vietata («gestione differita»).
Durante l’utilizzo dei veicoli per movimentazione interna l’operatore si concentra soprattutto sul processo di deposito e di prelievo. Poiché tali veicoli non possono mantenere una distanza di 0,50 m dalla scaffalatura (spazio sufficiente per il passaggio uomo), se i pedoni si trovassero nella corsia stretta contemporaneamente al veicolo incorrerebbero nel rischio di incidenti. Potenziali rischi residui in caso di mancata osservanza sono da escludere, ma la protezione individuale deve essere comunque garantita con l’utilizzo dei veicoli in corsia stretta, poiché le distanze di sicurezza non possono essere rispettate. ...
Figura 50 - Campi di rilevamento dei sistemi di protezione mobili e scanner laser con campo di rilevamento
... Equipaggiamento/Informazioni generali - Scanner ad elevate prestazioni per il monitoraggio dell’area di traslazione in direzione carico e direzione trazione - Sistema integrato nel computer di sicurezza. - Comando e funzione di visualizzazione mediante l’elemento di comando del veicolo - Comando e valutazione mediante l’impianto elettronico centrale del veicolo - Collegamento sicuro per CAN-Bus - Protocollo di sicurezza completo e certificato - Performance Level EN ISO 13849-1
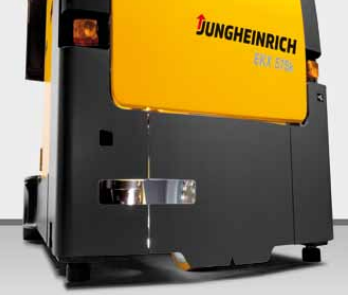
Figura 52 - Scanner laser integrato protetto ... 8. Ottimizzazione dei processi
Descrizione del sistema Con la navigazione di magazzino vengono utilizzate le potenzialità della tecnologia transponder per la navigazione e il raggiungimento assolutamente preciso dei posti pallet. Tutti gli ordini di trasporto o di commissionamento vengono inviati direttamente dal sistema gestione del magazzino via radio al terminale del veicolo. Da qui le coordinate X, Y e Z da raggiungere vengono acquisite tramite un’interfaccia seriale RS232 direttamente nella centralina del veicolo. In questo modo il veicolo conosce la posizione del ripiano di destinazione e il tragitto avviene quindi in maniera semiautomatica. Al conducente viene indicata dal display la direzione di marcia e sollevamento e, attivando le funzioni, il veicolo raggiunge la posizione desiderata autonomamente e con una precisione millimetrica. ...
L’operatore non ha più bisogno di occuparsi di:
- percorsi di avvicinamento, - ricerca pallet, - «momento ideale» per l’avvio della marcia diagonale, - scanner codici a barre come conferma al sistema di gestione magazzino (LVS) con carrelli combinati.
In questo modo l’operatore non è più responsabile della navigazione magazzino. Si escludono anche corse errate e di correzione.
Navigazione magazzino:
- Nel tempo più breve - Lungo il percorso più veloce - Con il minimo consumo energetico ...
Grazie all’avvio ottimizzato con la navigazione di magazzino è possibile un risparmio di tempo fino al 25 %. La «curva verde» mostra: Nel tempo più breve, lungo il percorso più veloce, con il minimo consumo energetico.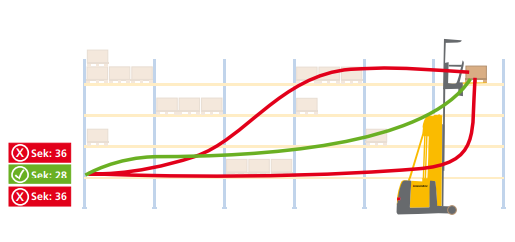
Figura 54 - Il confronto – carrello con/senza navigazione magazzino
Fonti:
Jungheinrich Italiana S.r.l - Opuscolo Magazzino a corsie strette VNA
EN ISO 3691-3:2017 Carrelli industriali - Requisiti di sicurezza e verifiche - Parte 3: Requisiti supplementari per carrelli con posto di guida elevabile e carrelli specificatamente progettati per circolare con carichi elevati EN 15878:2010 - Sistemi di stoccaggio statici di acciaio - Termini e definizioni EN 15512:2009 - Sistemi di stoccaggio statici di acciaio - Scaffalature portapallet - Principi per la progettazione strutturale EN 15620:2009 Sistemi di stoccaggio statici di acciaio - Scaffalature portapallet - Tolleranze, deformazioni e interspazi EN 15635:2009 Sistemi di stoccaggio statici di acciaio - Utilizzo e manutenzione dell'attrezzatura di immagazzinaggio EN 15629:2009 Sistemi di stoccaggio statici di acciaio - Specifiche dell'attrezzatura di immagazzinaggio EN 12845:2015 Installazioni fisse antincendio - Sistemi automatici a sprinkler - Progettazione, installazione e manutenzione EN 13813:2004 - Massetti e materiali per massetti - Materiali per massetti - Proprietà e requisiti. EN 206:2016 - Calcestruzzo - Specificazione, prestazione, produzione e conformità EN ISO 13849-1:2016 - Sicurezza del macchinario - Parti dei sistemi di comando legate alla sicurezza EN 62485-3:2016 Requisiti di sicurezza per batterie di accumulatori e loro installazioni Parte 3: Batterie di trazione, ISO 6292:2009 Carrelli industriali semoventi e trattori industriali - Capacità di frenatura e resistenza degli elementi del freno EN 1081:2001 Rivestimenti resilienti per pavimentazioni - Determinazione della resistenza elettrica
Altre
DIN 4102-X Comportamento al fuoco di materiali da costruzione DIN 1045-2 Strutture portanti in cemento, cemento armato e cemento precompresso DIN 18202 Tolleranze nell’edilizia DIN 1045 Costruzioni in acciaio e in cemento armato BGR 234 Direttiva dell’associazione di categoria, sistemi e apparecchiature da magazzino DIN 15185, parte 1 Sistemi di stoccaggio con carrelli industriali a guida fissa DIN 15185, parte 2 Sistemi di stoccaggio con carrelli industriali a guida fissa (protezione individuale per l’impiego di carrelli industriali nei magazzini a corsia stretta) Direttiva 2006/42/CE (Direttiva Macchine) Direttiva VDMA Requisiti pavimentazione per carrelli da corsia stretta FEM 4.005 (2013)
Premessa 1. Introduzione 2. I magazzini a corsie strette 3. Sistemi di guida 4. Scaffalature 5. Pavimentazione 6. Sistemi di assistenza alla guida. 7. Tecnologia RFID. 8 Sistemi di protezione individuale (PSS) 9. Ottimizzazione dei processi51 10. Gestione dell’energia e ricarica delle batterie 11 Checklist 12. Normativa/Direttive/Altre.
Certifico Srl - IT | REv. 00 2017 Pagine: 59 Formato: pdf Abbonati: Sicurezza/2X/3X/4X/Full
Info e download
|